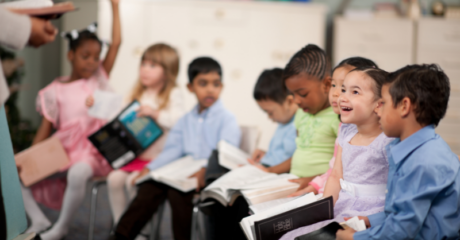
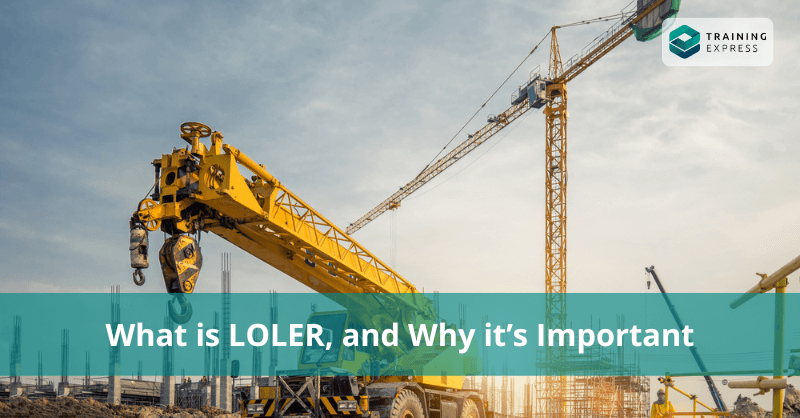
Table of Contents
What does LOLER Stand for?
What does LOLER stand for? LOLER is an acronym that stands for Lifting Operations and Lifting Equipment Regulations.
Besides, it is the Health & Safety Executive’s (HSE) official law for companies and people operating, owning, or controlling lifting equipment.
What is the Purpose of LOLER?
Lifting operations require specialist equipment to ensure work is undertaken efficiently and safely. Also, LOLER is also a guide to inspect that lifting equipment is fit to ensure its operators’ safety.
In addition, LOLER regulations require that a ‘competent person must properly plan all lifting operations’ and be appropriately supervised and carried out safely. Moreover, LOLER also requires you to carefully design every use of your equipment, considering all potential risks. Furthermore, you need to keep and maintain relevant safety records properly.
What is a Competent Person?
Under LOLER, a competent person has theoretical knowledge and practical experience in lifting equipment. Besides, they should be able to detect defects or weaknesses and assess their importance concerning the safety and regulations of the lifting equipment.
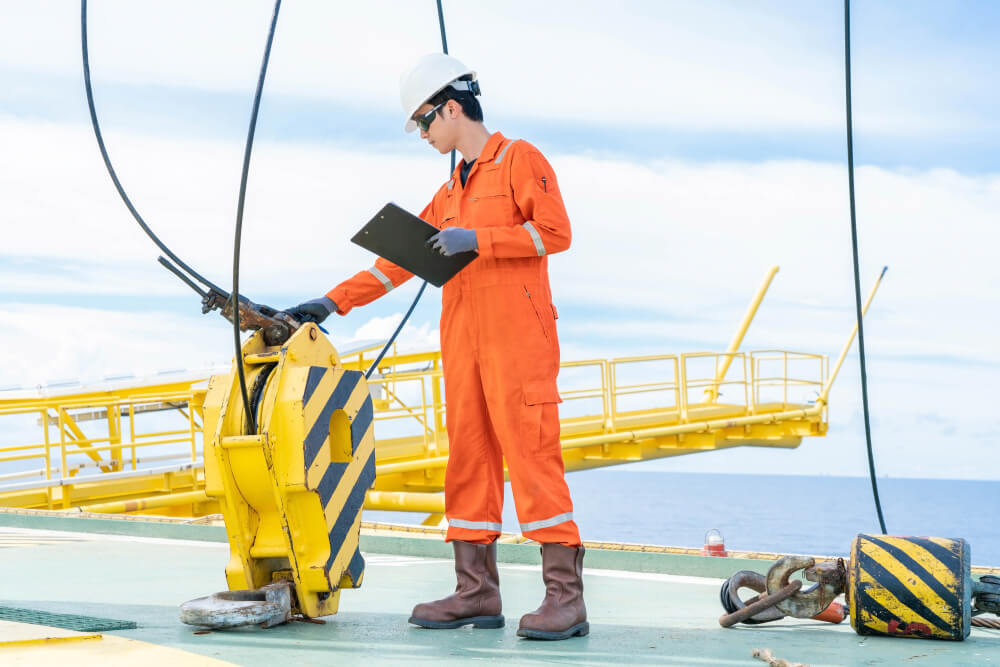
According to the HSE, a competent person:
- Firstly: a competent person is not the same person who executes routine maintenance.
- Secondly: should be impartial and independent enough to make accurate decisions.
In addition, regular lifting operations may be the duty of the people who perform them (for example crane operators or slingers). However, for considerably more difficult lifting operations (a tandem lift employing several cranes), a detailed plan should be prepared by a person with specialised competencies—enough training, knowledge, skills, and experience—appropriate for the complexity of the job.
What is a Lifting Operation?
A lifting operation is an operation that involves the lifting and lowering of a load. The load includes any material and people (or any combination) lifted by the lifting equipment.
In addition, you should conduct a lifting operation using lifting equipment or manually.
Moreover, LOLER makes sure you pick the right equipment when performing a lifting operation. Furthermore, manual lifting, putting down, carrying or moving, and holding is often called ‘manual handling of loads.
In this case, a comprehensive LOLER training course can help you become competent and deepen your understanding of safe lifting operations.
What is Lifting Equipment?
Lifting operations are necessary for any construction, manufacturing process, shipbuilding and ship-repairing. Lifting operations are a high-risk process that involves lifting equipment. For example
- Gantry cranes
- Overhead travelling cranes
- Crawler cranes
- Goods and passenger lifts
- Telehandlers and forklifts
- Tower cranes
- Powered hoists
- A building cleaning cradle and its suspension
- Lorry cranes (or lorry loaders)
- Jib cranes
- Motor vehicle lifts
- Vehicle tail lifts and cranes are appropriate for vehicles.
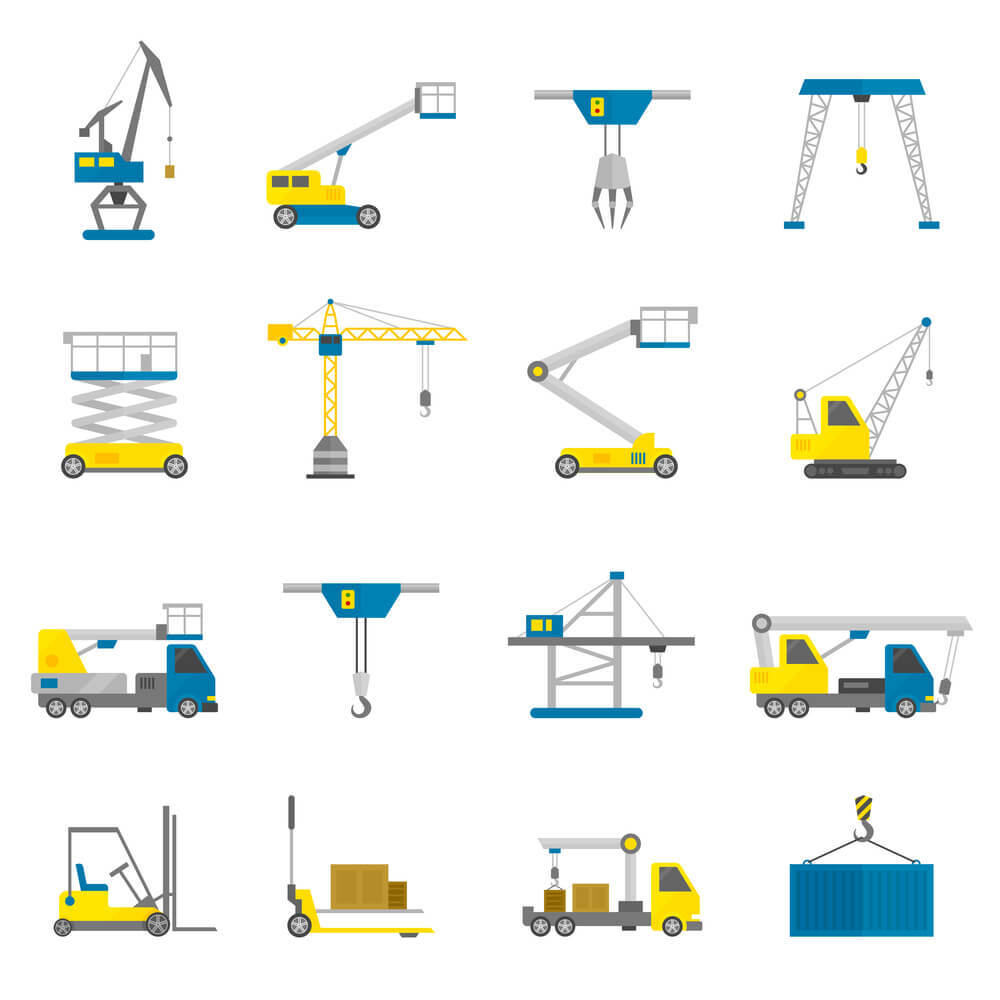
Selecting the Right Equipment
LOLER requires that lifting equipment have sufficient strength and stability. In addition, lifting equipment must be placed or installed correctly to reduce the risk in the workplace. Here is a quick direction to help you choose the perfect lifting equipment, including lifting hooks and lifting chains.- First: Assess your requirements & conditions
- Second: Enquire with experts
- Third: Consult with the workers or staff
- Fourth: Consider the equipment range
- Fifth: Choose reliable equipment.
- Finally: Consider regulatory conditions
Marking of Lifting Equipment
You need to mark lifting accessories and equipment for various reasons. The most significant is giving them a unique identity (ID). Moreover, the ID mark links the item and the documents registering its initial certification and in-service assessments. Furthermore, the initial certification will rely on local laws and regulations. Besides, lifting equipment not developed for lifting people must be marked to indicate that you should not use it to lift people. However, some items are manufactured in large batches, and every object in the set bears the same ID. So, there is a need for further marking to make the ID unique. In addition, manufacturing standards normally require the manufacturer to mark specific information about lifting equipment. This will include a batch number and the weight-related information of the parts.Planning, Organising and Carrying out Lifting Operations
According to LOLER, a competent person must adequately plan all lifting equipment-related tasks and carefully supervise workers to perform them safely. To clarify, in planning any lifting operation, assessing and identifying risks is essential to identify the most suitable method and equipment for the job. Lifting operations range from:- First: very simple operations, where trained, competent people design plans for minimal on-the-job to minimise risks.
- Second: very complex and challenging operations require detailed planning with high levels of input, supervision, and monitoring by professionals.
Thorough Examination
A thorough examination is a detailed and organised examination of lifting equipment by an expert or competent person. Besides, they are responsible for finding any issues that are harmful to workers or might become dangerous. Lifting equipment must be thoroughly examined in several situations, including- First: where it is exposed to conditions causing weakness, liable to result in danger
- Second: before first use and where it depends on installation at another site.
LOLER Examination
The Health and Safety Executive (HSE) defines a LOLER inspection as a comprehensive examination of lifting equipment by a “competent” or qualified person. It is often said that the LOLER examination and thorough examinations are the same.What Items Require Inspection or Thorough Examination under LOLER?
A LOLER thorough examination (LOLER regulation 9) should be conducted on all lifting equipment to comply with LOLER. In addition, It includes any equipment used at work for lowering or lifting loads and attachments used for fixing, supporting and anchoring them.Who Has Obligations and Responsibilities Under LOLER?
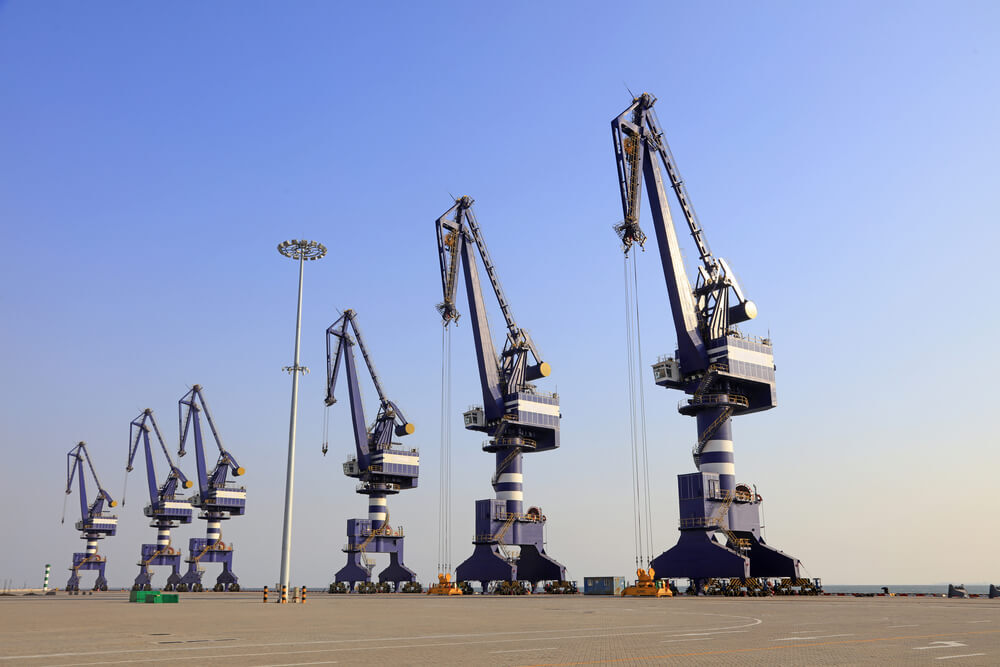
- First: a hired crane used at a building site
- Second: contract lift
- Third: vehicles used to collect rubbish.
- Four: Medical hoists
- Five: Container trucks
Lifting Equipment to which LOLER may Not Apply
You might notice that some lifting equipment is not essential or related to lifting work, such as roller shutter doors, stair lifts, escalators, fall arrest ropes, tipper trucks, etc. Therefore, LOLER may not apply to this type of equipment.
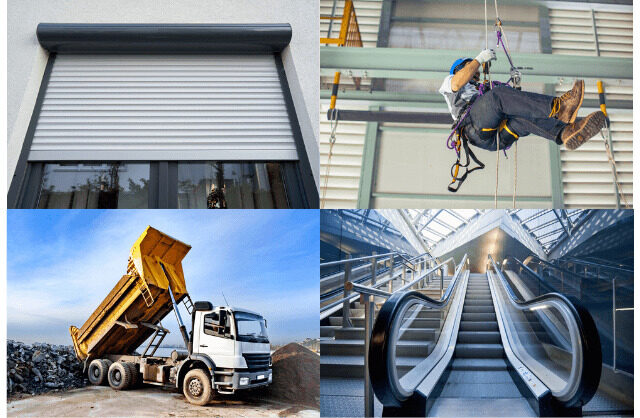
Planning Lifting Operations
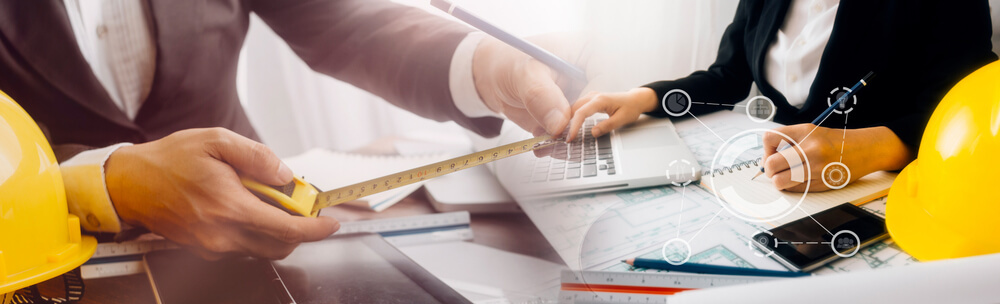
A single initial generic plan, for example, forklift trucks at a factory) may be necessary, which might be part of the regular risk assessment for the activity. However, you must evaluate the plan regularly to ensure that everything has stayed the same and that the strategy is still relevant.
In addition, depending on the circumstances, routine lifting operations that are a little more complex may need to be prepared each time the lifting process is conducted.
Another key fact to remember, any lifting operation plan must address the expected dangers related to the activity and determine the relevant resources (including personnel) required for the project to be completed safely. Along with LOLER, you should consider the relevant factors. For example:
- Visibility
- Overturning
- Proximity hazards
- Lifting people
- Overload
- Location
- Environment
- Derating
- Attaching/detaching and securing loads
- Continuing integrity of the equipment
Notably, the plan should set out the activities for each stage of the operation and identify the duties of those concerned.
LOLER Legislation
The purpose of the LOLER Legislation is to guarantee that workers conduct lifting activities as safely as possible. Moreover, it required the activities to be organised, coordinated and carried out safely by qualified and experienced individuals. Certainly, it is a duty call for employers.
Besides, you should ensure that all lifting tools fit the task and the records are up-to-date. Additionally, wherever you perform lifting operations, you should follow HSE suggestions, such as:
- First: Plan carefully
- Second: Ensure tasks are carried out by persons with the required skills and
- Third: Supervise properly to ensure that they are carried out safely.
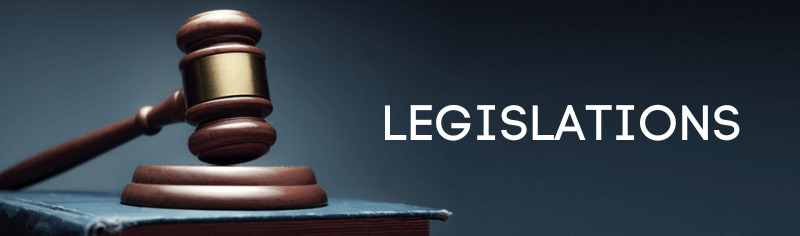
Other Legislation
Personal Protective Equipment at Work Regulations 1992
This legislation works towards lowering the risk of casualties by using the correct PPE. Of course, the employer must supply this. Another key fact to remember, it is the employee’s responsibility to use the PPE properly at the right time. Certainly, it is a duty call for employers.
The Provision and Use of Work Equipment Regulations 1998
PUWER suggest that any equipment or machinery must be appropriate for the purpose & that anyone operating the equipment supplied must be adequately trained.
PUWER or LOLER: Which is Best?
It is difficult to say which is best as both are applicable in different conditions. LOLER only applies to lift equipment, whereas PUWER applies to all equipment. However, it is essential to remember that lifting equipment is still classed as equipment so that you can apply both PUWER and LOLER. In addition, both PUWER and LOLER legislation recommends a post-installation inspection.
So, If you are working only with lifting equipment, you should focus on LOLER. However, if you have many kinds of equipment and lifting equipment, you should focus more on PUWER.
Therefore, both legislation can help prevent unnecessary mistakes and accidents. Don’t worry. You have the flexibility to follow any of them.
The Management of Health and Safety at Work Regulations 1999
The company or employers are responsible for carrying out risk assessments and inspecting them at the correct intervals, creating plans to prevent risks and keeping records.
They should also carry out health check-ups when necessary. In addition, You should assign a responsible person to help the organisation comply with the legal obligations.
The Supply of Machinery (Safety) Regulations 1992 – Machinery Directive
The regulations prohibit responsible persons from putting machinery on the GB market or using it unless it is safe. Additionally, they must also make sure that it complies with all relevant health and safety laws.
How to be Compliant With LOLER Regulations?
To maintain standards and comply with LOLER regulations, it’s essential that you thoroughly check and inspect lifting equipment at regular intervals (weekly/monthly/quarterly).
Besides, you need to follow the HSE suggestions to minimise risks in the workplace. In addition, the suggestions include planning, having the necessary skills & supervision.
The Effects of Not Complying with LOLER
Failure to comply with LOLER may have tragic consequences. You may face imprisonment, a fine or both. It is difficult to believe that, human life is the biggest cost of violating health and safety laws.
For instance, in 2012, a company manager in charge of lifting equipment was given a two-year prison sentence for violating LOLER legislation.
Another example: In 2016, a London-based crane hire company paid £750,000 as a fine as one of their cranes collapsed, and it caused the deaths of two people.
LOLER Certificates: Do I Need One for My Platform Lift?
Yes. A LOLER Certificate of thorough examination is a legal requirement of the Health and Safety at Work Act. In addition, it forms part of an employer’s responsibility to ensure overall compliance with the law (The Provision and Use of Work Equipment 1988 and The Lifting Operations and Lifting Equipment Regulations 1988.)
For instance, all passenger-carrying lifts must have a LOLER test and certification every six months by law. In addition, This includes all goods lifts and gartec platform lifts.
LOLER Inspection Frequency
Most lifting equipment will be subject to deterioration and need regular in-service inspections since adverse environmental conditions may cause further damage to the equipment. Therefore, HSE guidelines suggest conducting a thorough examination at the intervals recommended by LOLER (every 6 or 12 months, based on the equipment).Summary
To summarise, (LOLER) Lifting Operations and Lifting Equipment Regulations 1998 is official law for companies and people who own lifting equipment. Moreover, we cannot ignore that LOLER ensures you select the right equipment and perform routine maintenance to minimise risks as much as possible. Besides, lifting operations possess high risks and involve lifting equipment such as cranes and lifts. Notably, a competent person should thoroughly examine to comply with the LOLER legislation. For a better understanding of LOLER, check out our LOLER Training course.FAQ
Who is Responsible for Lifting Operation?
The employer or owner is responsible for lifting operations. Besides, they should ensure the safety and regular inspection of the lifting equipment.Can Anyone Do a Risk Assessment?
You should remember that you can only assess risks if you have the proper knowledge. Importantly, to carry out risk assessments, you must have relevant knowledge and skills. In addition, it is the employer’s duty, or he can appoint a competent person to do so.Do I Need a LOLER Inspection?
Yes. You should admit that the concept behind LOLER is to lower the risks to employees’ or workers’ health and safety from lifting equipment used at work. In addition, to comply with LOLER legislation, you must inspect and thoroughly examine lifting equipment every six to twelve months.
Learn More
- Available Courses
- Career Bundles73
- Animal care5
- Law8
- Quality Licence Scheme Endorsed111
- Teaching13
- Teaching & Academics Primary27
- Accounting & Finance Primary30
- Training3
- Design9
- IT & Software44
- Healthcare126
- Marketing31
- Health and Safety402
- Construction48
- Electronics25
- Hospitality22
- Health and Social Care219
- Child Psychology37
- Management377
- Business Skills268
- First Aid70
- Employability264
- Safeguarding75
- Food Hygiene103
- Personal Development1277