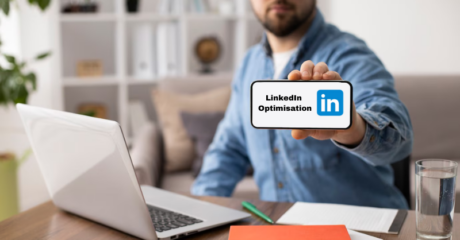
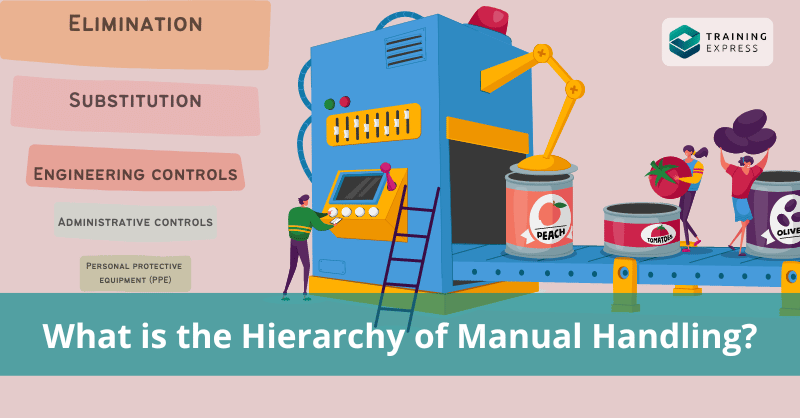
Injuries sustained as a result of manual handling may have far-reaching consequences. Heavy physical labour, awkward postures, repeated arms, legs, and back motions, and a history of injury may all enhance the likelihood of these hazards occurring on the job. What are we, then, expected to do? Well, we must assess the potential hazards posed by the job and implement appropriate safety precautions. To do that, we have to follow the hierarchy of manual handling. Therefore, we comprehensively analyse the hierarchy of manual handling in this article.
Table of Contents
What is Manual Handling?
Manual handling uses body forces to move or push objects and live animals. You may use your hands, legs, shoulders, or whole body to do manual handling. In essence, manual handling requires muscular strength. However, moving or pushing people from one position to another is not manual handling. Instead, it’s called moving and handling.
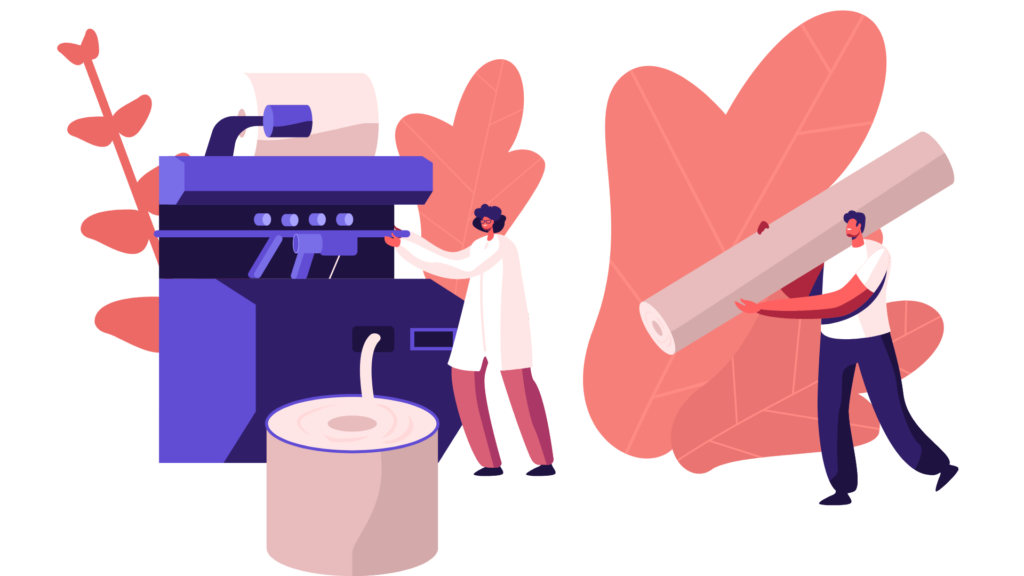
What are the Key areas of Manual Handling?
There are four key areas of manual handling. Those are TILE- Task, Individual, Load, and Environment.
Task
While doing manual handling, you will go through some tasks like lifting or pushing. Therefore, identifying each task is essential. For example, you may lift and carry instead of push or pull. On the other hand, another manual handling may require lowering your body.
In addition, a task may be repetitive or strenuous. Knowing the nature of tasks, you can decide your next move. So, “Task” is one of the key manual handling areas.
Individual
People in the workplace will perform the tasks. Managers assign one or more people to perform the tasks. Therefore, management should evaluate the appointed person for his capacity. For example, an unfit person may cause severe injuries to himself while doing the job.
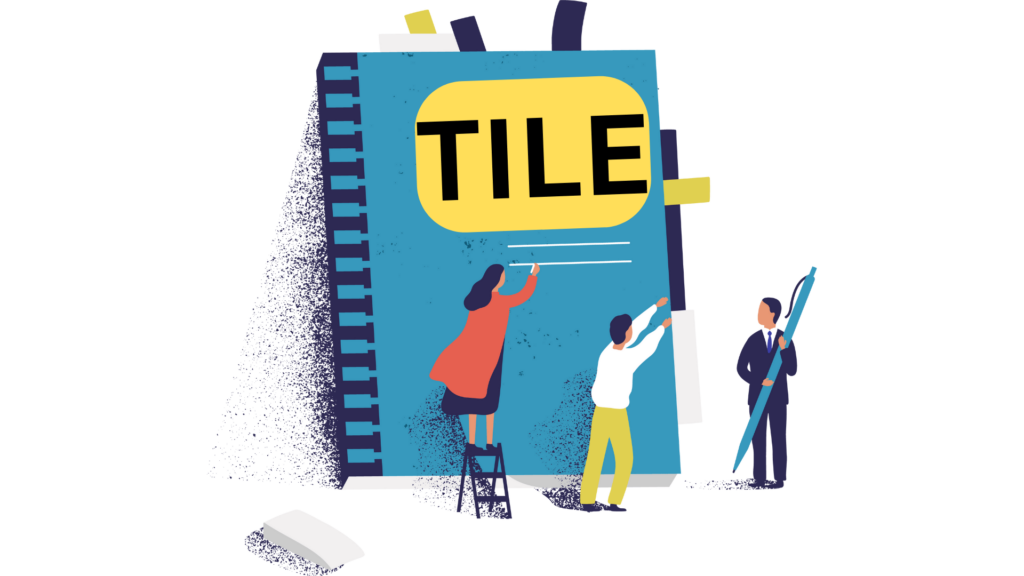
Load
The load means the object you push or carry. For example, suppose you and your coworker are moving a drum containing chemicals. In that case, both of you need to be careful.
The nature of the load plays a crucial role in safe manual handling. For example, the load may be heavier than your capacity or can be moved by a machine. However, workers cannot take a suitable method to carry the load if they don’t analyse its nature.
Environment
The environment is the condition of your surroundings when handling a load. For example, workers sometimes forget to check the floor or the whole area for hazards during manual handling. Obstructions such as cluttered floors will cause the individual to slip and fall. In addition, weather conditions play an essential role. No matter the cause, you shouldn’t forget to check your surroundings before performing a task.
Manual Handling Risk Assessment
When you cannot avoid risky manual handling, you need a suitable and adequate risk assessment. The assessment should pinpoint hazards or risk areas and suggest practical measures to lower them. In addition, use a checklist. It will enable you to assess each potential source of risk thoroughly. Furthermore, you may effectively identify risks and create practical solutions by involving workers and safety representatives in the risk assessment. Checklists will help emphasise the total degree of risk involved. In addition, they will show where and what changes are needed to lower the risk of harm and simplify it. Therefore, it will aid in prioritising the required corrective activities.Risks of Improper Manual Handling
Lack of adherence to the hierarchy of manual handling leads to improper manual handling. According to HSE, improper manual handling procedures are to blame for nearly a third of all workplace accidents.MSDs
Musculoskeletal Diseases (MSDs) result from routinely performing tasks like heavy lifting. Improper manual handling impacts muscles, bones, and joints. Statistically, over 200 musculoskeletal diseases affect 25% of the population in the UK. The annual cost of MSD to the UK is 10.8 million workdays.Back Pain
Improper manual handling causes back pain. For example, back pain may result from prolonged hunching or stooping. Back pain can range in severity from minor to chronic. As a result, it becomes difficult to work and maintain a healthy lifestyle.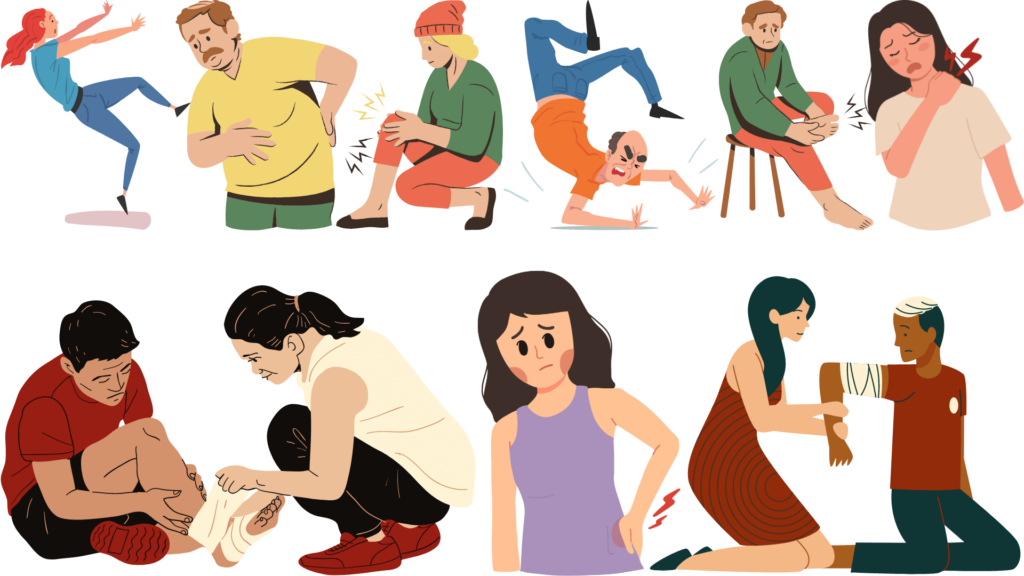
Hernias
Heavy lifting can result in hernias. The risk increases with age. In addition, you may require surgery to treat a hernia. A hernia occurs when an internal organ pushes through a muscle or tissue weakness. Different hernias exist. All can lead to excruciating pain if left untreated.
Hand and Foot Injuries
Hand injuries are common in manual handling. When handling hazardous objects, your hands are in danger. On the other hand, large loads frequently fall on workers’ feet, but workers hardly ever lift using their feet. All in all, fractures in the hands and feet can result from improper manual handling.
Strains and Sprains
Occupational strains and sprains happen to falls, slips, and trips. In addition, if you perform repetitive work and lift heavy loads, you may face them. As a result, the muscles, tendons, or ligaments are in pain.
To avoid such consequences, take our Manual Handling Training Course and sharpen your manual handling skills.
What is the Hierarchy of Control?
The hierarchy of control is a structure of measures. You probably have ideas in your mind about controlling hazards in the workplace. In addition, you know what is causing manual handling hazards. However, all these ideas in your mind need to be structured into a coherent framework. The hierarchy of control provides that framework. It consists of Elimination, Substitution, Engineering Controls, Administrative Controls, and Personal Protective Equipments (PPEs).
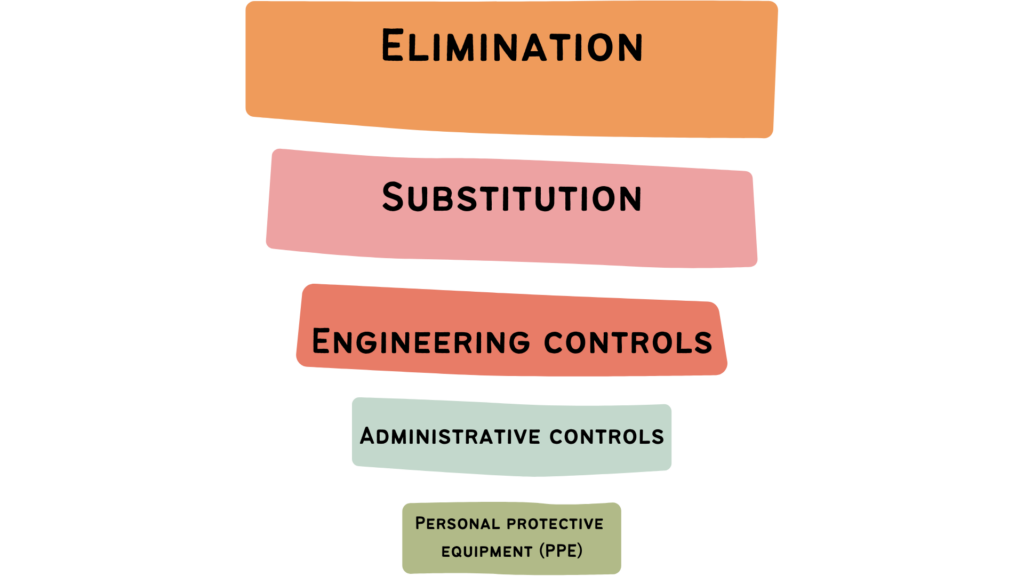
What is the Manual Handling Hierarchy of Controls?
Protecting workers is crucial to limit their exposure to risks at work. However, risks frequently occur in manual handling too. So, it’s better to use the hierarchy of manual handling controls and determine which activities best control manual handling hazards. We have got five tiers of activities to lessen or eliminate hazards. As the hierarchy of manual handling, each activity plays a unique part in managing risks.
Elimination

The first control in the hierarchy of manual handling is Elimination, such as halting the entire work process or stopping the formation of a hazard. For example, you can divide large objects into smaller ones before lifting them. In addition, you may avoid using a sharp tool while doing a task. Also, you can NOT do the manual handling at all. Instead, you may use automation to perform the task.
Since it eliminates the hazard from the core, Elimination is the first and best option. Let’s look into some Elimination Controls in the hierarchy of manual handling.
- Termination of a particular manual handling task.
- Contract with a specialist team to do the manual handling instead of doing it yourself.
- Halting the whole manual handling process.
- Dividing an enormous load into smaller ones.
- Avoidance in using hazardous materials.
- Introducing automation and machines to the workplace.
- Stop the ongoing work as soon as you notice any unusual activity or formation of hazards.
Substitution
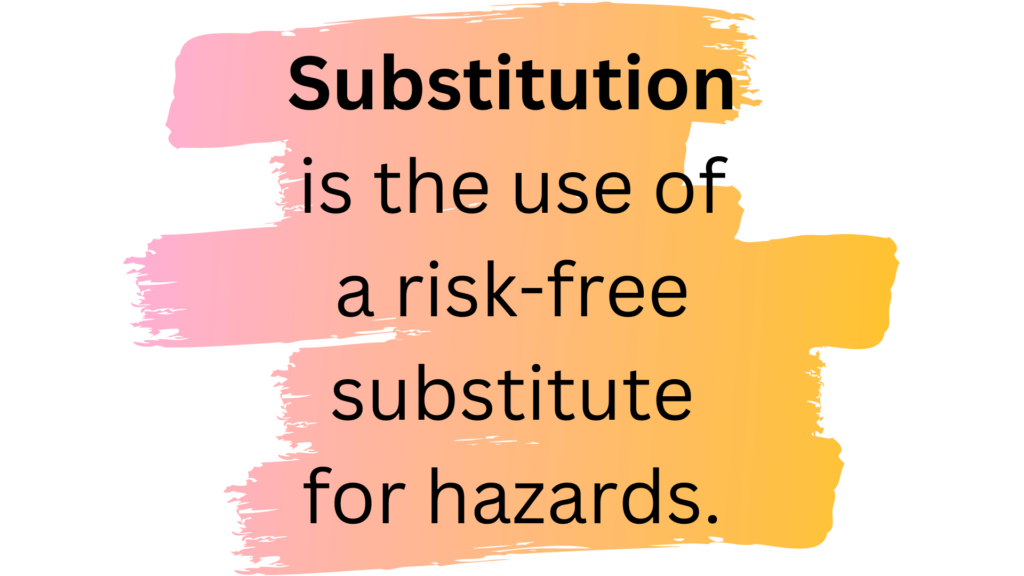
Substitution is the second control of the hierarchy of manual handling. You can change a process or a load entirely and place a new one. However, it’s crucial to weigh the potential new hazards of a replacement against the existing ones when considering one. In addition, how the replacement will work with other workers may be a concern. Adequate substitution minimises the possibility of negative consequences and does not introduce additional hazards.
Let’s look into some Substitution Controls in the hierarchy of manual handling.
- Changing your arm or shoulder position.
- Using a trolley instead of directly lifting the load.
- Giving up odd body positions and maintaining a straightforward stance.
- Replacing a pulling task with a pushing one.
- Changing the load weight.
- Moving hazardous chemicals to safer containers.
Engineering Controls
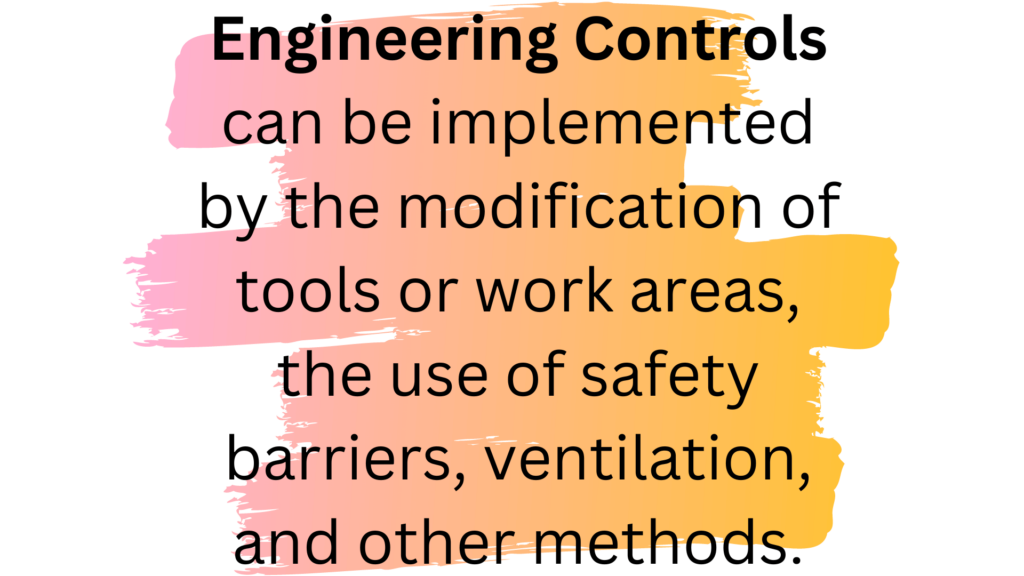
Engineering Controls is the third among the hierarchy of manual handling. It lessens or stops workers from being exposed to hazards. The best controls follow the original equipment design. The controls must be operated with little user input to function appropriately without hindering or complicating the work process. They should also eliminate or block the hazard at its source before it comes into touch with the worker.
Let’s look into some Engineering Controls in the hierarchy of manual handling.
- To Keep the Floor as Clear as Possible and Reduce Trip Risks
You can rearrange the places where deliveries are unloaded. In addition, you may change the areas where specific products are housed. On the other hand, you can remove any debris or infrequently used machinery from a location.
Workers have got to keep the area organised and scrupulously clean. In that way, hazards on all fronts will be less. Manual handling will be far less necessary.
- Making Use of Mechanical Lifting Tools or Equipment
You might be able to employ lifting equipment to move loads. As a result, it’ll eliminate the need for staff to perform manual handling, depending on the required handling.
There is a significant requirement for forklifts, stair climbers, and pallet trucks when working in manufacturing or warehousing. These ease manual handling and offer a simple way to securely lift and move large goods.
- Employee-Pushed Trolleys and Non-Powered Trucks
Non-powered equipment isn’t mechanical and requires less training. So, workers using them are at lesser risk. However, some training is still necessary to lower the danger of hazards.
- Manual Handling of Animals
When working as a vet, you will need manual handling to move or lift them. For example, vet workers may move mice by using a handling tunnel. Workers will lift them inside and then transport them to their destination. Engineering Controls are necessary in such cases. Also, you may use a HIAB crane, telehandler, or equivalent lifting device to perform manual handling on sheep or other big animals.
Administrative Controls
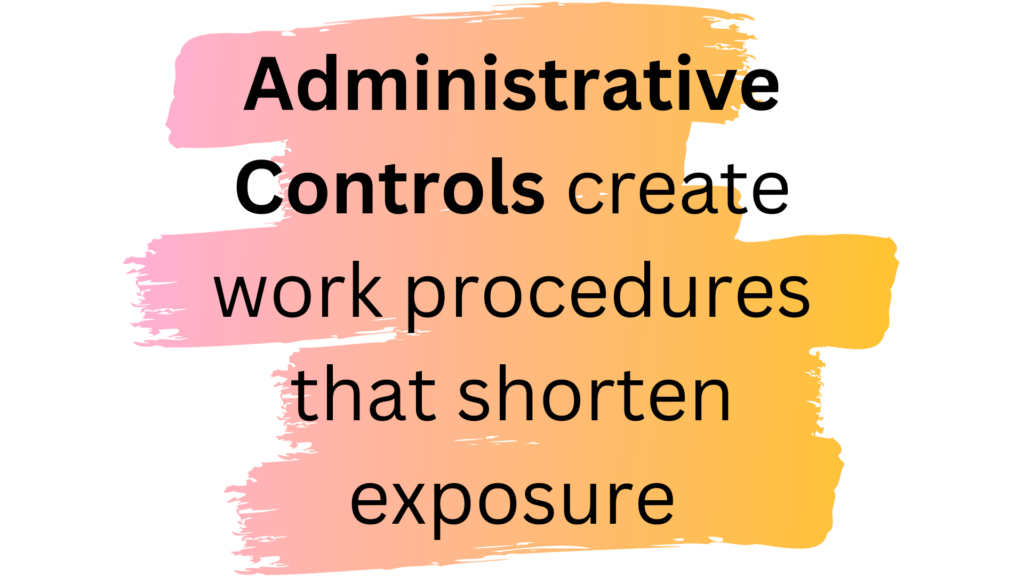
Administrative Controls is the fourth control in the hierarchy of manual handling. It creates work procedures that shorten exposure to risks in terms of time, frequency, or intensity. For example, these controls might comprise of
- job rotation,
- proper rest breaks,
- access restrictions to machinery or hazard areas,
- line speed adjustments,
- and work process training.
Let’s look into some Administrative Controls in the hierarchy of manual handling.
- A Good Working Framework for Workers
Safe manual handling requires managers to understand how workers function. In addition, it’s necessary to meet their requirements effectively. Therefore, creating a good framework in the workplace is a part of Administrative Controls.
- Training and Development
Workers need access to training and instruction to complete the tasks safely. Therefore, manual handling training sessions are crucial when it’s a common component of daily work.
- Prevention of Fatigue
Fatigue is one of the dangers connected to manual handling. Workers will experience fatigue if they engage in repetitive or heavy manual handling tasks. Therefore, Administrative Controls give routine breaks to workers. As a result, people get well-rested and perform manual handling with the least amount of hazards in the workplace.
Personal Protective Equipment (PPE)
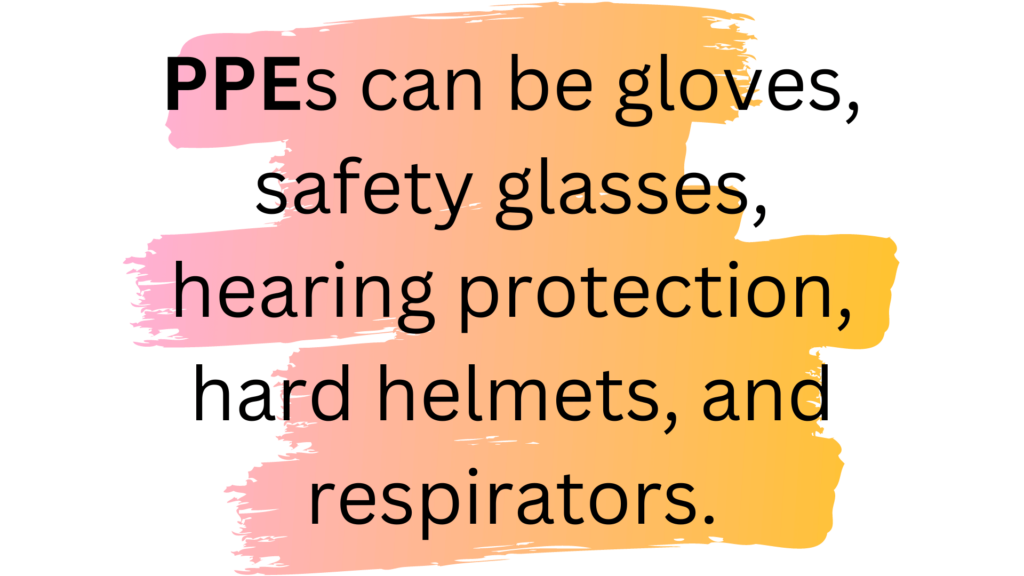
PPE is the last option in the hierarchy of manual handling to reduce exposure to risks. Remember, when more efficient control alternatives are available, relying solely on PPE to manage hazards is not ideal. Therefore, it will be beneficial only when workers utilise PPE correctly and regularly. Also, PPE may appear less expensive than other controls, but costs can increase over time. It’s especially true when used daily for several workers. Let’s look into some PPE Controls in the hierarchy of manual handling.
- PPE Training Programme
Employers must arrange a PPE training programme when workers use PPE. In addition, the training programme will monitor the efficacy of PPE, selection and usage, and inspection and replacement of damaged or worn-out PPE.
- Unavailability of Other Control Options
PPE is the sole available control option. In the meantime, you are developing other controls. However, other measures cannot sufficiently decrease the risk of exposure, and you can introduce PPE.
How to Implement Elimination and Substitution?
It might be challenging to implement Elimination and Substitution into an existing process. However, these techniques function best when applied during the design or development phases of a task, location, or tool. In addition, Elimination and Substitution may be the most straightforward and affordable strategy throughout the development stage. Furthermore, applying Elimination and Substitution is a good idea when you choose new tools or methods. A proactive approach to incorporating prevention into the design of workspaces, tools, operations, and places is known as “Prevention Through Design”.
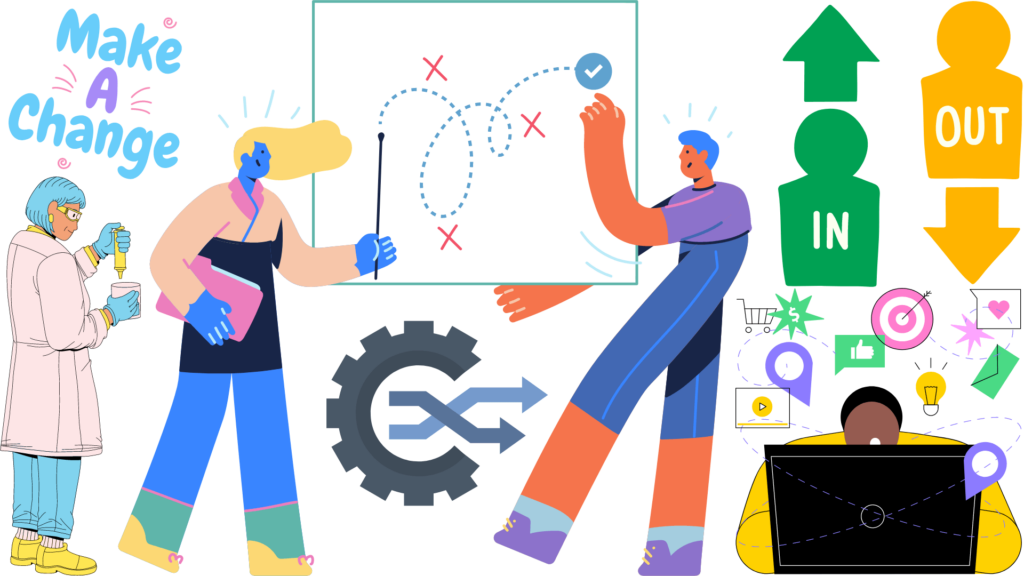
FAQS
You may ask the manager or yourself some obvious questions during a manual handling task. We’ll provide the answers to such questions.
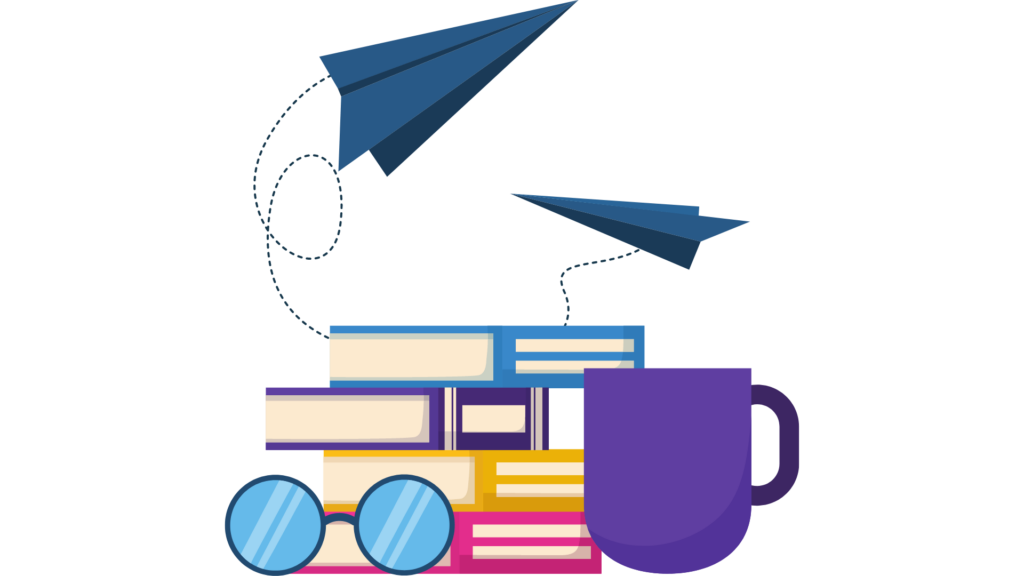
What are the Steps of Manual Handling?
The steps of manual handling are as follows:
- Make a lift plan.
Ensure the item is easy to lift, stable, and unlikely to move or shift. Eliminate obstacles; make sure the path is open, and there is room to lower the burden wherever you intend to move it.
- Set your feet in place.
Keep your feet apart to have a stable and balanced foundation for lifting. You have a solid foundation to begin your manual handling exercise while standing with your feet apart.
- Be sure to stand straight.
To keep a secure posture throughout the lift, be prepared to move your feet. It may be more difficult to wear tight apparel or shoes like high heels or flip-flops. When raising anything from a low position, bend your knees but keep your back straight to retain its natural curve.
- Maintain a tight grip.
Be careful to keep your arms within the space your legs define for you. A hook grip is easier to maintain than keeping your fingers straight while holding onto anything.
- Lift smoothly.
To maintain control of your head, lift your chin as you start the lift. Once the burden has been grasped, look forward rather than down at it.
- Staying close to the load.
If at all possible, embrace the load close to your body. It should help you lift the load with more strength and stability than if you grip it securely with your hands. Hold the burden close to your body for as long as you can, with the heavier side facing you.
- Lay it down before adjusting it.
Put the load down first, then manoeuvre it into the proper position if you need to place it in a specific location.
What should You Take into Consideration in Manual Handling?
There are four things you must think about. First, the specifics of the manual handling. Second, the size and composition of the load to be carried. Third, the skill level of the person doing the work. Fourthly, the context in which the action is being taken.
Is Engineering Controls a Viable Option?
Engineering controls may be more expensive upfront than administrative or PPE controls. However, long-term running expenses are typically cheaper, particularly when numerous workers are protected. Engineering controls also have the potential to reduce costs in other aspects of the work process or facility operation.
For further information, take a look at the Manual Handling Training Course we offer.
Summary
The hierarchy of manual handling is a set of tiers or levels for safe handling. You’ve undoubtedly given some thought to the topic of minimising workplace dangers. In addition, you understand the factors that contribute to manual handling risks. You must organise your scattered thoughts into some form. The control hierarchy offers this structure.
The Controls may involve using PPEs or managing workers and the environment. Overall, the hierarchy of manual handling helps you figure out what measures you need to take to reduce the risk of injury. Finally, get the hang of the hierarchy of manual handling by taking our Manual Handling Training Course.
- Available Courses
- Marketing34
- Charity & Non-Profit Courses26
- Job Ready Programme29
- Animal care10
- Law11
- Quality Licence Scheme Endorsed111
- Teaching16
- Teaching & Academics Primary29
- Accounting & Finance Primary37
- Training5
- Design23
- IT & Software196
- Healthcare135
- Health and Safety431
- Career Bundles133
- Construction53
- Electronics30
- Hospitality27
- Health and Social Care251
- Child Psychology39
- Management389
- Business Skills285
- First Aid75
- Employability270
- Safeguarding78
- Food Hygiene107
- Personal Development1419