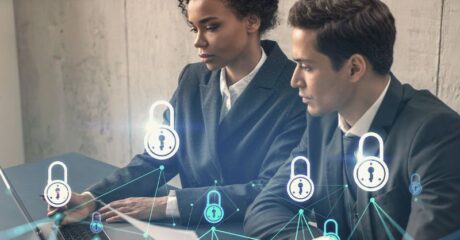
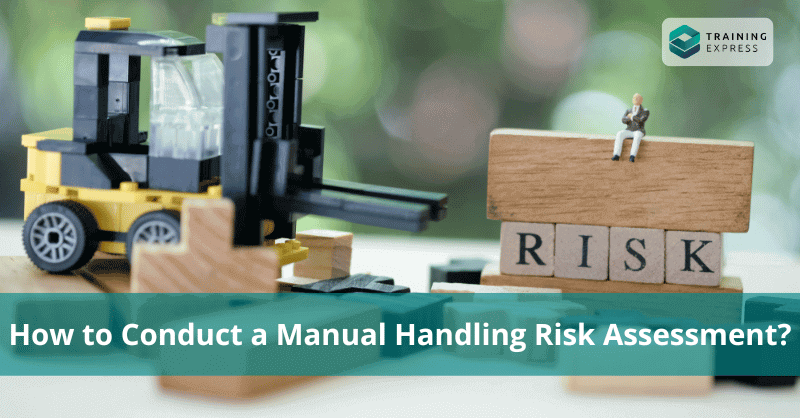
There are many risk factors when carrying out manual handling, lifting, moving or pulling tasks. Any one of them could result in risks, perhaps serious injury. As a result, all organisation or company is accountable for manual handling risk assessment to ensure safety in the workplace.
Table of Contents
What is Manual Handling
Manual handling means transporting, supporting or carrying a load by hand or physical force. Moreover, it includes pushing, pulling, lifting, putting down or moving loads. In addition, a load can be an object, person, or animal.
What are the Risks of Manual Handling?
Manual handling risks include back injuries, strains, sprains, crush injuries, fractures, musculoskeletal disorders, trapped fingers and cuts from sharp objects, etc. Besides, manual handling is the leading cause of work-related musculoskeletal disorders, accounting for over a third of workplace accidents.
In addition, musculoskeletal disorders cover a wide range of problems and pain in the upper limbs, shoulders, neck, arms, hips, legs and back.
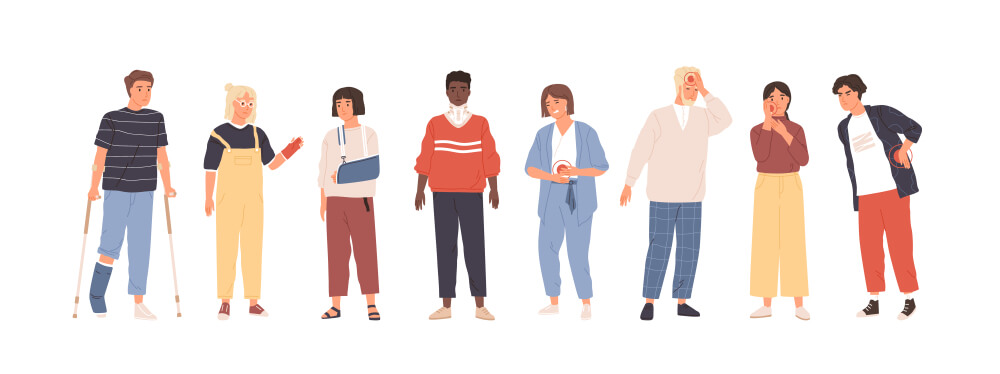
What is Risk Assessment in Moving and Handling?
Moving and handling risk assessments help determine where risks could happen and how to prevent them. In addition, it includes different kinds of physical injuries.
Manual Handling Risk Assessment Examples
Imagine Company ABC wants to conduct a manual handling risk assessment. It has 20 workers, including a physically disabled person. Besides, the office has attached kitchen, toilets and washing facilities on each floor. And, there is no fire safety for an emergency.
To identify and solve potential hazards, the employer of ABC company ‘Jack’ is performing these duties:
- First, walking around the office, noting things that might cause a threat;
- Second, marking the workers with disabilities who cannot perform specific tasks;
- Third, talking to managers and workers to understand their concerns and complaints;
- Fourth, taking measures to stop fire risks in an emergency;
- Fifth, taking notes from previous hazard experiences and reviewing the improvements.
This is just an example. You don’t have to follow each of them in every situation. In fact, you can perform different actions depending on different situations. However, remember these steps as basics.
Why are Risk Assessments Needed in Manual Handling?
Employers in every industry are legally instructed to protect their contractors, employees, customers and site visitors from injuries. Besides, you need to conduct a manual handling risk assessment to identify risks in manual handling tasks and develop measures to prevent those risks.
Moreover, the evaluation must consider the people doing it, the kind of load and the environment in which the task takes place. And the objective of risk assessments is to improve workplace health and safety.
In addition, risk assessments should create awareness about hazards and risks. Therefore, the risk assessment strategy must identify workplace threats and eliminate the risks. Finally, it should communicate health and safety information to employees.
How to Conduct a Manual Handling Risk Assessment?
You can follow FIVE steps when carrying out a manual handling risk assessment. They are:
Task Description
Collect details on how you want to conduct a specific task. Besides, consider the four risk factors:
Technical information such as the weight of the load, physical dimensions, and postures you observe during the action. Besides, assessing the amount of workspace available and the task duration. It could be the load which is too heavy, workers are handling the load at an unsafe height. And it may cause the body to be uncomfortable. Besides, you need to gather enough evidence to support the identified risk factors. Once you have identified a specific risk, you need to evaluate the possible solutions to solve it. Additionally, you need to follow the manual handling risk assessment steps. Collect Technical Information
Identify the Risks
What are the Ways of Handling an Identified Risk During a Risk Assessment?
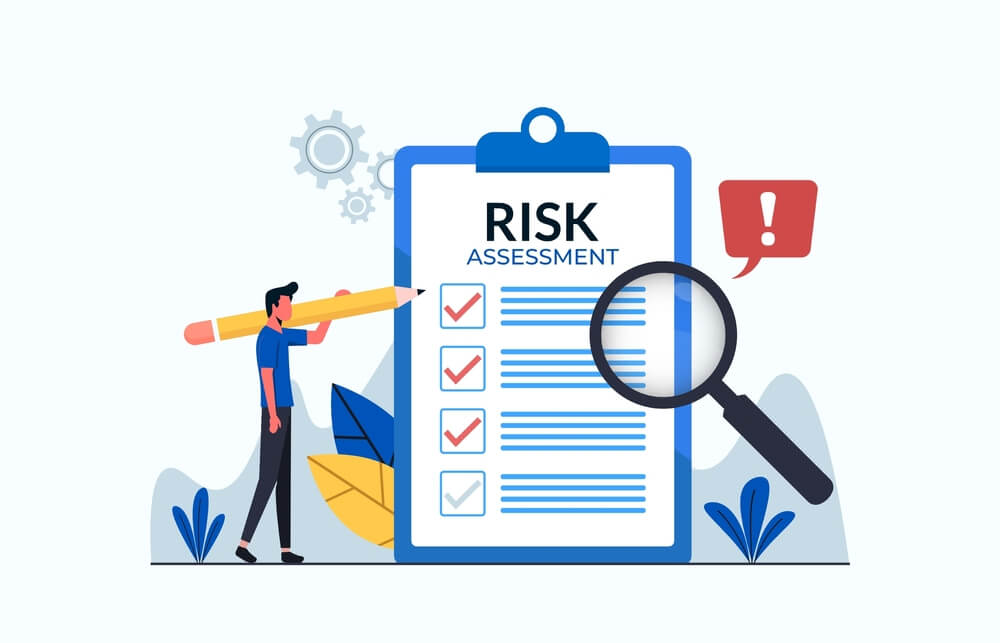
You should identify what is causing you trouble. Then, think about who will be harmed. And this evaluation will help you decide where to reduce the risk level and which threats you should prioritise first. Finally, treat the risk and review the improvements.
Identify the Areas for Improvement
Now it’s time to initiate improvement actions. In addition, this step needs clear communication with staff and reviewing the information gathered. Moreover, the improvements put in place should reduce the risk of injury and may include the following:
- First, the use of mechanical support for all or part of the activity,
- Secondly, reorganisation of work areas or elements,
- Thirdly, where manual handling will take place, instruction in safe lift techniques,
- Finally, the development of a protection system and work plan.
What are the Key Areas that Should be Considered During a Manual Handling Risk Assessment?
There are four key areas that you need to consider during a manual handling risk assessment.
They are:
- The task,
- Individual capability,
- The load,
- The working environment.
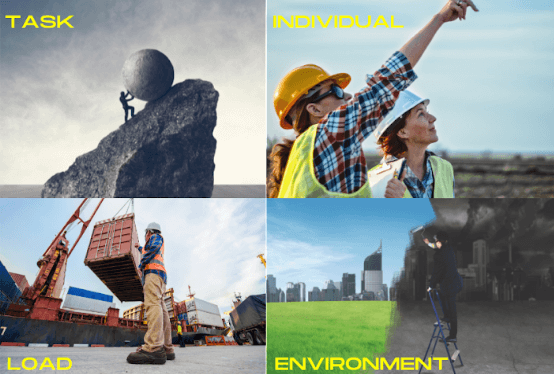
Remember the acronym ”TILE”, which stands for Task, Individual, Load and Environment.
Review the Changes
This could involve simple checks to ensure that lifting techniques are performed with the instructions. Besides, you need to check if proper handling resources are available or not.
Manual Handling Risk Assessment Checklist
The manual handling risk assessment checklist includes all risks related information regarding the Task, Load, Individual and Environment.
Besides, the list shows how mild or severe a particular risk is. In addition, there are check boxes for the frequency of movement, mechanical support, persons at risk, and actions taken to control the risks. And workers and employees can tick the boxes according to the risk factors and situations.
Here is a demo:
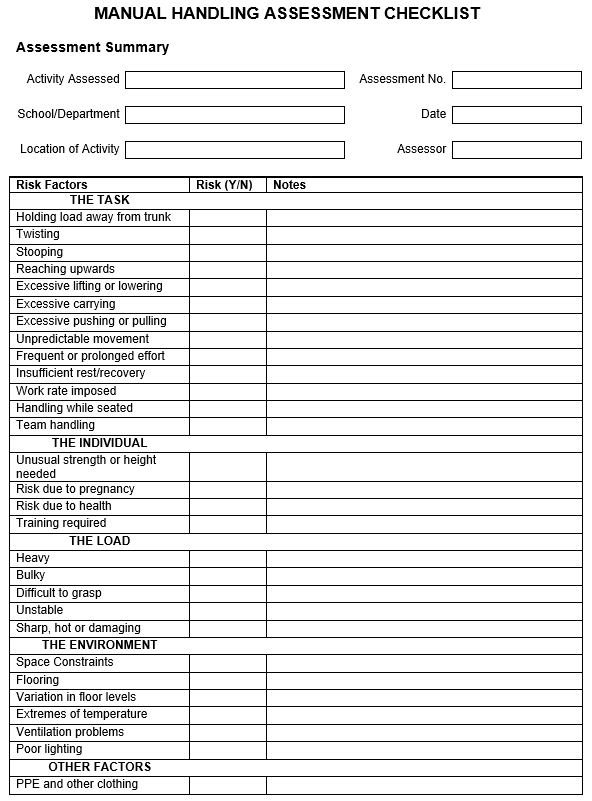
What to do After a Manual Handling Risk Assessment?
Once the manual handling risk assessment has been completed, you should take action to eliminate or reduce the risks. Actions you can perform:
The employer is responsible for conducting a manual handling risk assessment. Moreover, an employer should evaluate all manual handling assignments that pose risks or injuries to workers. In addition, employees must take proper care of their own health and safety. The employer must avoid Manual Handling as reasonably possible if there is a chance of injury. If this cannot be done, they must reduce the risk of injury as much as possible. Moreover, the employee should monitor carefully if an employee complains of discomfort. Besides, the Manual Handling Operations Regulations (MHOR) – regulation 4(1) sets out a hierarchy of actions to reduce manual handling risks. Employees are also responsible for keeping an eye on their health and safety. Therefore, they must communicate with their employers to fulfil their health and safety duties. Employees should obey some instructions, such as There is no fixed timetable for performing a manual handling risk assessment. So, employers can do manual handling risk assessments periodically or whenever situations demand. In addition, there should also be regular monitoring to observe moving and handling activities to ensure correct methods, techniques and equipment are utilised. Besides, employers should carry it out whenever workers report manual handling injuries.Who is Responsible for Conducting a Manual Handling Risk Assessment?
Employer Responsibilities for Manual Handling Risk Assessments
Employee Responsibilities for Manual Handling Risk Assessments
How Often Should a Manual Handling Risk Assessment Be Done?
The Law Regarding Manual Handling Risk Assessments

The Law Regarding Manual Handling risk assessments is the Manual Handling Operations Regulations 1992 (MHOR). The law sets out some regulations and roles for employers and employees to reduce the risks in the workplace.
Therefore, employers must comply with their legal obligations. Also, employers face considerable fines or imprisonment for breaking health and safety legislation. In addition, employees also need to correspond with the law and safety protocols.
Summary
You don’t know what risks are waiting for you. But you can take some precautions to protect yourself in such circumstances. Similarly, an employer or employee can assess manual handling risks regularly to minimise potential hazards and injuries in the workplace.
Besides, manual handling risk assessments are critical as they are integral to an occupational health and safety control plan. Indeed, they help to create awareness regarding hazards and risks for employees, employers, and the public.
Also, you can check our Manual handling training course for in-depth understanding.
- Available Courses
- Level 7,Development,IT & Software,Quality Licence Scheme Endorsed1
- Training3
- Accounting & Finance Primary30
- Teaching & Academics Primary27
- Teaching13
- Quality Licence Scheme Endorsed111
- Law8
- Animal care5
- Intermediate,Development,Intermediate,IT & Software3
- Intermediate,IT & Software8
- Design9
- Advanced,Development,IT & Software,Others1
- Intermediate,IT & Software,Others1
- Level 4,Development,IT & Software,Quality Licence Scheme Endorsed1
- Intermediate,CPD Accredited,IT & Software,Personal Development1
- Intermediate,IT & Software,Personal Development2
- Intermediate,Development,IT & Software1
- Level 2,Development,IT & Software,Quality Licence Scheme Endorsed1
- Intermediate,Employability,Intermediate,IT & Software,Personal Development1
- Intermediate,Design,IT & Software1
- Hospitality22
- Personal Development1277
- Food Hygiene103
- Safeguarding75
- Employability264
- First Aid70
- Business Skills268
- Management377
- Child Psychology37
- Health and Social Care219
- Health and Safety402
- Electronics25
- Construction48
- Career Bundles73
- Marketing31
- Healthcare126
- IT & Software44