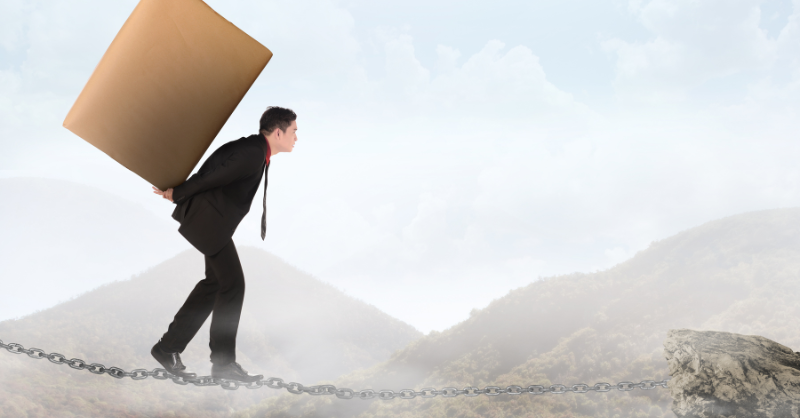
Small businesses face unique challenges when it comes to managing their inventory effectively. One such challenge is the need for auto replenishment systems that can streamline the inventory replenishment process and ensure that businesses have the right amount of stock at the right time.
Manual inventory management requires significant time and effort. Employees who could be focusing on customer service, sales, or other important tasks might be tied up in manual stock-checking and ordering processes. Inconsistent stock levels can lead to customer dissatisfaction or, on the contrary, additional costs. If customers frequently encounter out-of-stock situations, they might perceive the business as unreliable, negatively impacting its reputation. Let’s explore small businesses’ challenges in implementing auto replenishment systems and provide practical solutions to overcome them.
Challenges of Implementing Auto Replenishment Systems
While Auto Replenishment Systems can offer efficiency and cost-saving advantages in retail, small businesses may hesitate to adopt them due to cost concerns, complexity, fears of overstocking, limited product variety, strong supplier relationships, data accuracy issues, and resistance to change. Here is a list of potential challenges with implementing Auto Replinishem that can be solved with nothing but a deliberate approach to implementation.Inaccurate Inventory Data
Accurate inventory data is essential for effective auto replenishment. However, small businesses often struggle with inaccurate inventory data due to human error, outdated manual processes, or issues with their inventory management systems. This can lead to stockouts, overstocking, and poor customer service. To mitigate this challenge, small businesses can invest in inventory management software that provides real-time tracking and accurate reporting of inventory levels. Implementing barcode scanning systems can also help minimize the risk of human error and improve the accuracy of inventory data. Regular physical inventory counts can further ensure that inventory data is up-to-date and reliable.Poor Inventory Visibility
Poor inventory visibility can impede the auto replenishment process, making it difficult to monitor inventory levels and make informed purchasing decisions. Small businesses, especially those with multiple locations or suppliers, often struggle with obtaining real-time visibility into their inventory. To address this challenge, small businesses can implement real-time inventory tracking systems that provide continuous updates on inventory levels. Utilizing RFID technology and inventory management software can also help improve inventory visibility and reduce the risk of errors or discrepancies in inventory data. With better visibility, businesses can make more accurate decisions regarding inventory replenishment.Manual Inventory Management Processes
Managing inventory manually can be time-consuming and prone to errors. Small businesses often lack the resources to dedicate to manual inventory management processes, which can hinder the auto replenishment process and lead to inefficiencies. Small businesses should consider automating their inventory management processes to overcome this challenge. By implementing inventory management software and utilizing mobile-based inventory management apps, businesses can streamline their inventory management workflows and reduce the time spent on manual tasks. Barcode scanning systems can also help automate data entry and improve the accuracy of inventory records.Choosing the Right Replenishment Strategy
Selecting the right replenishment strategy is crucial for the success of the auto replenishment process. Small businesses must carefully evaluate customer demand, market trends, and financial goals to determine the most effective replenishment strategy. To address this challenge, small businesses can analyze sales data to identify which products are selling well and which are not. Implementing an ABC inventory classification system can help prioritize products based on their demand and value. Additionally, gathering customer feedback can provide valuable insights into customer preferences and help inform purchasing decisions. Modern tools offering data-driven replenishment recommendations can further optimize the strategy.Lack of Expertise
Implementing auto replenishment systems requires expertise in inventory management and technology. Small businesses often lack the necessary knowledge and experience to effectively implement and manage these systems. To overcome this challenge, small businesses can seek external expertise by partnering with inventory management consultants or leveraging the support services provided by inventory management software vendors. These experts can provide guidance on system implementation, offer training for employees, and ensure that the auto replenishment system is tailored to the specific needs of the business.Conclusion
Implementing auto replenishment systems can significantly improve the efficiency and profitability of small businesses. By addressing the challenges of stockouts, overstocking, inaccurate inventory data, poor inventory visibility, manual processes, choosing the right replenishment strategy, and lack of expertise, small businesses can optimize their auto replenishment process and ensure that they have the right amount of stock at the right time.Get Certified at Training Express
Training Express offer a range of excellent compliance training & certification courses suitable for everyone.
- Available Courses
- Law10
- IT & Software225
- Design28
- Training6
- Accounting & Finance Primary48
- Teaching & Academics Primary36
- Teaching22
- Quality Licence Scheme Endorsed160
- Healthcare169
- Animal care10
- Job Ready Programme52
- Charity & Non-Profit Courses28
- HR & Leadership4
- Administration & Office Skills2
- Mandatory Training36
- Regulated Courses4
- Health and Safety520
- Marketing38
- Career Bundles201
- Construction59
- Electronics31
- Hospitality28
- Health and Social Care289
- Child Psychology40
- Management423
- Business Skills292
- First Aid73
- Employability283
- Safeguarding79
- Food Hygiene116
- Personal Development1597